The growing emphasis on Aluminum Composite Panels (ACP) has led to becoming the go-to solution, irrespective of interior and exterior cladding requirements in present-day construction practices. ACP sheets are renowned for their strength, durability, and visual appeal, and their versatile nature allows them to be used in both residential and commercial constructions. However, it is a difficult balancing act for producers to produce high-quality ACPs at reasonable prices.
Panels that are both aesthetically pleasing and resistant to weather, fire, and wear & tear constitute the market demands. Customers also anticipate these qualities at affordable prices. This has led manufacturers to develop innovative ways to reduce costs without sacrificing quality. Considering the stark competition and narrow profit margins, striking an ideal balance between the two remains critical, especially considering profitability and reliability.
Through adopting new practices, state-of-the-art emerging technologies and strategic interventions, this balance can be achieved indefinitely. Let’s take a look at five practical tactics that producers use to strike a healthy balance between quality and cost-effectiveness in ACP production.
Reduce Waste for Enhanced Efficiency
A key component of efficient, high-quality manufacturing is waste reduction. Manufacturers can drastically cut down on material waste by using sophisticated machinery and accurate production procedures. This lowers production costs and improves the quality of the final product. Regular audits and lean manufacturing concepts aid in finding inefficiencies and optimizing production procedures.
In addition to lowering disposal costs, recycling scrap materials and implementing eco-friendly practices improve sustainability. According to studies, lean manufacturing techniques can drastically increase cost efficiency by cutting waste by as much as 20–30%. By emphasizing waste reduction, manufacturers lower expenses and solidify their standing as leaders in the eco-friendly sector, attracting clients who care about the environment.
Innovative Design and Strategic Inventory Management
Profitability and operational efficiency are significantly impacted by efficient inventory and product design management. Based on sales trends, manufacturers can categorize inventory into "Runner," "Repeater," and "Stranger" products. Production and stock levels for repeater and runner products should be prioritized in order to avoid overstocking slow-moving inventory, which lowers storage and interest expenses. By matching regional demand patterns, regional inventory planning ensures quicker order fulfilment and further optimizes stock management. Effective inventory control can improve cash flow and profitability by reducing carrying costs by 15–25%. A balanced product line is guaranteed, overproduction is avoided, and overall cash flow is improved by strategic inventory management.
Continuous Production and Coating Line Integration
Efficiency and quality depend on streamlined production procedures backed by cutting-edge continuous production and coating lines. Planning a process is made easy by integrated operations, which also removes delays and disruptions. Work-in-progress accumulation is minimized and bottlenecks are reduced thanks to modern machinery that guarantees materials flow efficiently. Continuous manufacturing systems guarantee consistent product quality, cut down on production time, and save material expenses. By increasing throughput by 10% to 20%, continuous production systems allow orders to be completed more quickly without sacrificing quality. With this strategy, manufacturers may efficiently increase their operations while upholding high standards for their products.
Preventive Maintenance and Machine Monitoring
Maintaining manufacturing efficiency and guaranteeing constant product quality depends heavily on well-maintained equipment. By reducing unplanned malfunctions, scheduled preventive maintenance lowers downtime and related repair expenses. Systems for tracking machine performance in real-time allow for the early identification of possible problems and the avoidance of expensive interruptions. Maintaining equipment properly also extends its lifespan, lowering the need for frequent replacements and guaranteeing effective output. Machine lifespan can be increased by up to 30% and maintenance expenses can be decreased by 15% to 20% with preventive maintenance. Manufacturers protect long-term cost efficiency by increasing productivity and lowering operational hazards through investments in machine monitoring and preventative maintenance.
Leverage Advanced Technology for Competitive Edge
Modern technology is revolutionizing the way that ACP manufacture balances quality and cost. Repetitive process automation lowers labour costs, guarantees accuracy, and minimizes errors. Modern coating techniques, including 3-Coat 2-Bake method, improve items' longevity and visual attractiveness while providing consumers with higher-quality goods. Additionally, data analytics are essential for demand forecasting, manufacturing schedule optimization, overproduction avoidance, and order fulfilment on time. Businesses that use automation and cutting-edge technology report consistent product quality and an average 25–30% increase in production efficiency. By implementing cutting-edge technologies, producers may produce high-quality goods quickly and effectively, maintaining their competitiveness in a market that is changing quickly.
Conclusion
Innovation, cutting-edge technology, and strategic planning are all necessary to balance quality and cost-effectiveness in ACP manufacturing. Manufacturers like can attain operational excellence by concentrating on waste reduction, inventory optimization, integrating continuous production lines, maintaining machinery, and utilizing state-of-the-art technologies. These tactics not only guarantee cost-effectiveness but also enhance product quality, allowing firms to satisfy consumer demands and maintain their standing as reliable market leaders. Adopting these strategies is crucial for long-term success, profitability, and steady growth in the fast-paced industry of today.
Authored By;
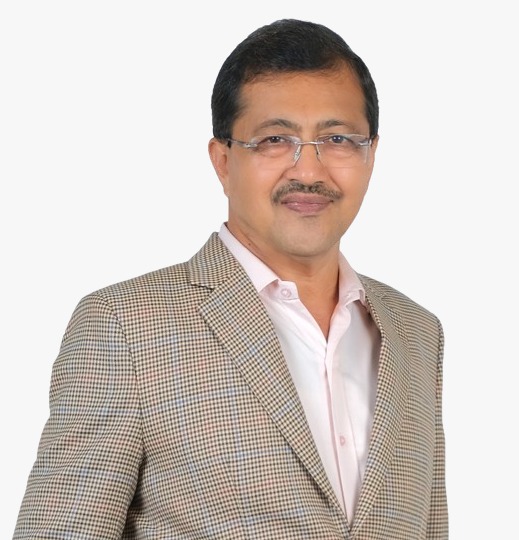